- Runs on Windows® 7 and Windows Server 2008 operating systems
- Uses the same Studio 5000® environment and Logix control engine as other Logix platforms
- Includes platform independence (whitebox, industrial computer, etc.).
- Provides connection to open networks, including EtherNet/IP™, ControlNet™, and DeviceNet™
- Offers customization of data access, virtual backplane toolkit for integration of third party networks or specialty modules
- Supports multiple I/O interfaces
- Provides ability to develop custom C programs to integrate via external routines
Hi, I have this problem, when I try to open SoftLogix Chassis Monitor I see this picture, if someone could help me please. It would appear your copy of SoftLogix 5800 is not properly activated. Since Activation Support from Rockwell is free I'd advise calling the number or using their website and do a free chat. Softlogix Chassis Monitor. Resolving this condition requires removing the SoftLogix Ethernet module from the Chassis Monitor, and then re-insert the Softlogix Ethernet module once the power to the Ethernet switch has been restored. We will step through the setup of SoftLogix Chassis Monitor and the configuration of our SoftLogix controller. From the SoftLogix chassis monitor. The chassis monitor shows the 1789-SIM module as a virtual module in the SoftLogix chassis. Anyone use Rockwell's Softlogix? You have to build the rack in the SoftLogix Chassis Monitor and then build the rack in RSLogix to match. SoftLogix Chassis modules must be removed'. How am i going to get out of this. To invoke the RSLinx GUI, remove all SoftLogix controllers from the chassis monitor and use the RSLinx Control Panel to start RSLinx software as an application instead of a service. Before you can install the SoftLogix 5800 controller, you need to perform the following steps. Problems with installing SoftLogix 5800 Hi, new to PLC's and this subreddit. I recently tried to install SoftLogix 5800 to use with RS Logix5000/RSLinx and I cannot seem to open the actual chassis monitor.
1789-L10 SoftLogix™ Controllers
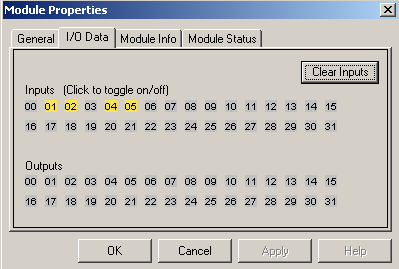
- One controller
- Memory size limit of 2 MB per controller
- Two PCI network interface cards
- One EtherNet/IP card
- One 1784-SIM module
- No third-party virtual backplane module support
- Three-slot virtual chassis
1789-L30 SoftLogix Controllers
- Two controllers
- Memory size limit of 64 MB per controller
- Five PCI network interface cards
- One 1784-SIM module
- Third-party virtual backplane module support
- Five-slot virtual chassis


Allen Bradley Softlogix
1789-L60 SoftLogix Controllers
Softlogix Chassis Monitoring System
- Six controllers
- Memory size limit of 64 MB per controller
- 16 PCI network interface cards
- 16 1784-SIM modules
- Third-party virtual backplane module support
- 16-slot virtual chassis
sorry but I can’t personally help you with your “installation” problem - because I’ve never worked with either RSLogix Emulate or SoftLogix ...
but here’s a thought ... why do you need either one of those packages to “test an RSView HMI” application? ... I’ve always had EXCELLENT results from using the following technique ...
suppose that you’re animating a display of a tank to show the liquid level rising and falling based on a numerical value in the PLC ... suppose that the tag is named TANK_LEVEL ... instead of setting this up as a “Device” type tag, just set it up (temporarily) as a “Memory” type tag ...
now while you’re working on your graphics, etc. just put a small (temporary) “Numeric Input” object on your window - and tie that to the TANK_LEVEL tag ... now you can manually enter any value that you desire into the tag - and check out the operation of your screen animation ...
you can get fancier of course by using a temporary horizontal or vertical “slider” to more easily change the value ...
fancier yet: try using the same types techniques used in the RSView “Samples” application ... specifically, check out how the value of the tag “AutomotiveMotion” is automatically incremented in the “Derived Tags” section under “Logic and Control” ...
basic idea: whatever software you’re trying to use to “emulate” the PLC is probably going to take at least as much trouble (if not MORE) to properly simulate a series of variables as the techniques I’m recommending ... of course after the initial design work is done, you’ll still have to reassign your tags from “Memory” to “Device” before you put the system into operation in the field - but as long as you work systematically and carefully, that shouldn’t be too hard to do ...
finally ... in SOME cases you can actually go ahead and assign your tags directly as “Device” type and use the same techniques I’ve mentioned to manually adjust the values during the development phase of your project ... try experimenting with a few tags to get started ... secret handshake: USUALLY you can go to the “Node” setup screen and temporarily turn off the “Enabled” checkbox ... then you can USUALLY manually adjust the tag values yourself ...
then again, there’s the distinct possibility that I’ve misunderstood exactly WHY you’re trying to emulate the PLC in the first place ... if so, feel free to ignore all of this ... good luck with your project ...